HOME | DD
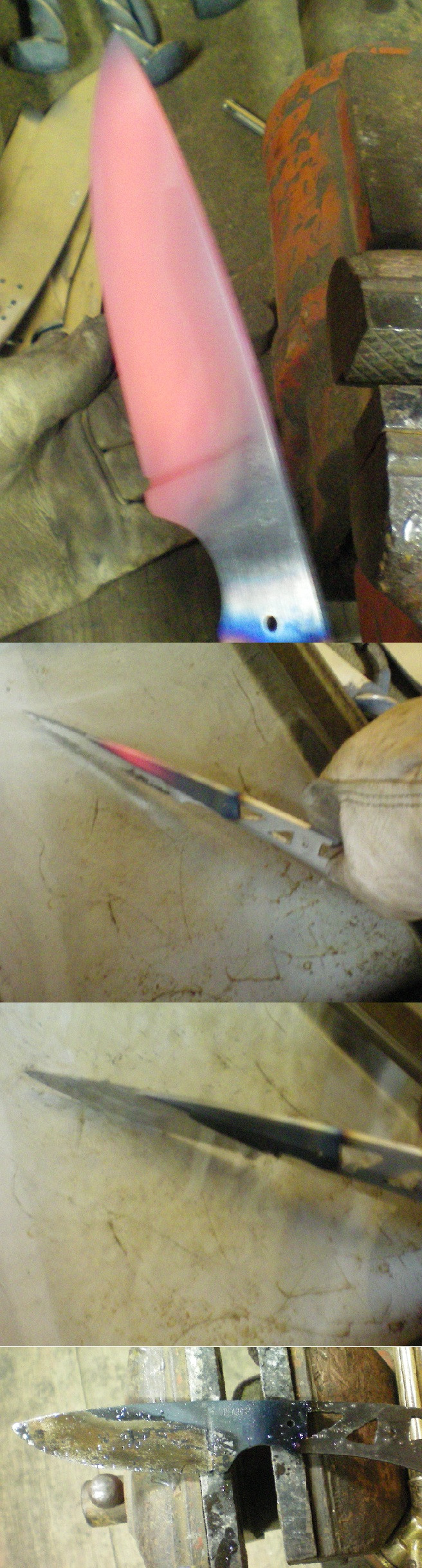
Published: 2011-10-14 13:26:40 +0000 UTC; Views: 4710; Favourites: 12; Downloads: 39
Redirect to original
Description
Previous Step: [link]Step 2: Hardening
To harden carbon steel, tool steel, and stainless steel you have to get the knife to critical temperature and then rapidly cool it, which is called quenching. But quenching is more commonly referred to when using a liquid for hardening rather than air.
Again, different metals require different processes to harden. Which means you will have different temperatures to take your metal to, with different heat soaking times, and you will have to use either water, oil, or air to get the best result. There is also quenching brine, but we will stick with the three that are most common.
Air Hardening: Steels like the A series and D-2 tool steels fall under this. Depending on the size, we use air to cool the metal. In some cases Air Hardening can be the same process as normalizing carbon steel, but in other cases it is air blasting the metal to reduce the temperature.
Water Quenching: W series, 10XX series for the most part can be water hardened, along with lower level carbon content metals. While there are metals that can be water hardened, most are considered oil hardening metals because of the fact that water could crack the blade. This process is more common in low carbon leveled metals, but its also used in higher leveled as well. It's wise to test your metal in water and oil first. Water give more of a hard quench, which could be disastrous for a knife. An example is these: [link] while I did get them hotter than I should have, the result could have been prevented if I had used oil. Depending on the metal you can heat the water or leave it at room temperature.
Oil Quenching: O-1, L-6, 5160, 10XX series fall under this type. It feels more forgiving to the touchier metals. Most of them are suggested to heat the oil up before quenching. I suppose I could go into detail about how the structure and density of the oil vs water can make all the difference in the world. But who really wants to read all that?
I do a triple hardening cycle on all of my knives. Since I'm doing carbon steel, I will be using oil to quench my metal.
First thing I do is put the torch in the vise like so: [link]
You want to take your time with the heat. Allow the entire blade to be blue before taking it to critical temperature. The reason I say this is because there is a chance, if you heat the blade to quickly, you could shock the steel and it could crack. At the very least heating it to fast could warp your blade. So make sure to get the whole knife warm, hot, then go to critical just to be on the safe side.
I start with the thickest part of my knife first and then when we get past the dark blue color, then I focus more on the blade, because I am going for a defined hamon line, by means of differential hardening.
The reason I keep the torch in the vise for this part, is turning it off and then loosening the vise will waste my heat. If I were doing 1095, which needs to be cooled within the second, I would miss my chance of hardening the blade. Plus this makes it less hassle.
I have my mineral oil heated to about 120F. I like to check to make sure that the oil bath will cover at least 1/2 of the height of the blade for a solid edge harden.
I like to keep a magnet close to check the knife and make sure that the knife has reached non-magnetic temperature. It isn't in the picture, because with my free hand, I'm using the camera.
Once the knife is at critical temperature, I edge quench the knife I count to 7 before I submerge the entire knife in the oil. Once it is submerged, I count to 10 before taking it out of the mineral oil and dipping it in room temperature water until the knife is completely cooled off.
I then repeat this same process two more times. After the third cycle, the knife will look similar to the bottom picture.
Usually I don't even bother sanding the knife at this point. I take a rag or paper towel and clean off the knife and continue on to tempering.
Next Step: [link]
www.pearceknives.com <- For all those times that stabbing people to death with spoons took too long.
Logan Pearce
www.pearceknives.com
Facebook-> [link]
Related content
Comments: 12
BigEvilWolf [2012-04-03 14:43:24 +0000 UTC]
what eould be your advice, where should i harden my iron knife (its not stainless)? maybe in oil, so it wouldnt get rusty?
👍: 0 ⏩: 1
Logan-Pearce In reply to BigEvilWolf [2012-04-09 03:31:31 +0000 UTC]
It will still get rusty, even stainless steel will rust. It's just stain-less, not stain proof. I can't tell you how to harden your knife without knowing what metal it is. Like 1080, 5160, etc. Just saying that it's an iron knife, doesn't give me the amount of information that I need to be of any help.
If you don't know what type of steel it is, then the best thing to do is test small pieces of it. Cut off a small piece and test it in oil and see if it hardens, if not then test it in water, and so on.
I hope this helps and sorry I could be of more.
👍: 0 ⏩: 1
BigEvilWolf In reply to Logan-Pearce [2012-04-09 09:05:20 +0000 UTC]
thanks, and i dont know what kind of steel it is because i found it in my grandfathers village.
👍: 0 ⏩: 0
clsc [2011-10-18 23:13:56 +0000 UTC]
I'm a n00b to this, so excuse me for a second: Are there different types of mineral oil? Which types should be used or avoided? Thanks
👍: 0 ⏩: 1
Logan-Pearce In reply to clsc [2011-10-19 07:33:42 +0000 UTC]
Yep. There's three different classes of mineral oil. As far as I know you can use any of them for quenching. The only kind that I can get locally are the regular laxative mineral oil for people and the veterinarian grade. I usually chose the vet grade over people, but the difference isn't anything noticeable.
👍: 0 ⏩: 0
MindsEye56 [2011-10-15 01:54:25 +0000 UTC]
We went lightly over brine quenching in my welding fab classes but never used it, that would be considered sand and different materials containing carbon right?
👍: 0 ⏩: 1
Logan-Pearce In reply to MindsEye56 [2011-10-15 16:19:50 +0000 UTC]
I believe there are different types of brine. The only one I've ever really messed was a water based brine that had a sizable amount of sodium chloride in it.
👍: 0 ⏩: 0
Gin-Kusanagi [2011-10-14 22:49:25 +0000 UTC]
Isn't it actually possible to increase the carbon content through quenching?
👍: 0 ⏩: 1
Logan-Pearce In reply to Gin-Kusanagi [2011-10-14 23:21:00 +0000 UTC]
You can carbonize/carburise metal to put more carbon into metal. The process is a long one though.
When quenching high carbon metal the austenites turn into martensite, making the carbon on the outer layer of the knife harder. And the core stays tough.
If you use a coal fire, the coal will transfer some of the carbon content into the metal. It will also, put impurities in the metal as well though.
👍: 0 ⏩: 0
Mitchel-Jacobsen [2011-10-14 16:06:27 +0000 UTC]
" I suppose I could go into detail about how the structure and density of the oil vs water can make all the difference in the world. But who really wants to read all that?" I do I do I do!
yours looks pretty clean after coming out, mine always look scaly and crap.
👍: 0 ⏩: 1
Logan-Pearce In reply to Mitchel-Jacobsen [2011-10-15 00:20:37 +0000 UTC]
Basically all you need to know about the difference between the two are the abilities to cool off steel faster. Which I should have put that. It goes Brine-> Water -> Oil -> Air. Brine cooling the fastest and air cooling the slowest.
👍: 0 ⏩: 1
Mitchel-Jacobsen In reply to Logan-Pearce [2011-10-15 00:36:34 +0000 UTC]
I knew that, but I was kind of interested in the actual physics of it... I should take a metallurgy class.
👍: 0 ⏩: 0