HOME | DD
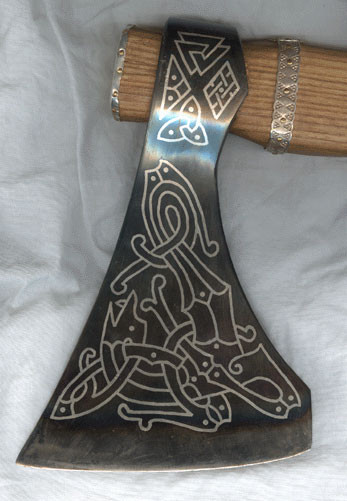
Published: 2005-03-21 06:59:47 +0000 UTC; Views: 20181; Favourites: 611; Downloads: 282
Redirect to original
Description
These three pictures are of differnt views of a large inlaid ax, made of steel, and ashwood, and decorated with silver. The patterns on the head were made by carving out channels in the steel, and then cutting them to a dovetail crossection, so that they are wider at the bottom than at the top. I then drew out silver wire to a thickness that would just fit into the channels. Fitting each piece of wire into position, I drove the silver into the channels, so as to cause it to spread out into the dovetail, and become perminantly atached. After all the pattern was so worked I filed and sanded the surface and hafted the ax with a handel I carved from an ash log. The designs are inspired by the inlay work of northern Europe in the 10th and 11th centuries.Related content
Comments: 282
barnsdalebob [2012-06-07 20:10:17 +0000 UTC]
very impressive thank for sharing and giving inspiration to try the more difficult aspects of our art.
👍: 0 ⏩: 0
Ross-Makoske [2011-02-03 18:10:05 +0000 UTC]
Cool! I like the Nordic symbols near the shaft.
👍: 0 ⏩: 0
Aranglinn [2010-11-30 15:40:08 +0000 UTC]
really amazing work!
but... how do you carve steel?
👍: 0 ⏩: 0
DOTO [2010-01-02 19:46:40 +0000 UTC]
That is really nicely done! I have got to have a go at inlays.
👍: 0 ⏩: 0
Vegvisir [2009-03-20 12:45:11 +0000 UTC]
Very impressive and authentic work!!! I appreciate this level of skill and the dedication to do such fine work. It's beautiful and inspiring!!! Could be very useful for removing heads too!
👍: 0 ⏩: 1
willofthewisp In reply to Vegvisir [2009-03-20 18:57:38 +0000 UTC]
Thanks that one was the third attempt. On the first I was learning the technique, and the design came out crude looking. The second ax looked beautiful, but felt clumsy and heavy so I sold it. On the third try everything came together and this one moves like running water and hits like stone falling from a cliff.
👍: 0 ⏩: 1
Vegvisir In reply to willofthewisp [2009-03-22 14:16:18 +0000 UTC]
You're welcome! You are not only skilled but dedicated brother!
Metalwork is rewarding!
👍: 0 ⏩: 1
taika-kim [2009-02-27 16:42:47 +0000 UTC]
Great! I tried inlaying recently, but didn't manage to manufacture a good engraver... So I'm now thinking of buying some proper ones, so I can make copies.
I recently found a book about engraving, and all the angles & such seem pretty specific :/
But I will definitely still try...
Did you make your own chisels btw?
👍: 0 ⏩: 1
willofthewisp In reply to taika-kim [2009-02-27 20:50:43 +0000 UTC]
If you are interested in inlay work, I have a few tips for you. Before you spend a bunch of money on tools, I would suggest borrowing a copy of "The Art of Engraving" by James Meek. There really isn't a good book that I have found on inlay, but his book has a good chapter on the subject, and a lot of advice about tools. The price of that book has been coming down for some time now, but it is still almost fifty bucks. If you make your own gravers, I recommend using W-1 drill rod. It is shipped fully annealed, can be cold worked to a certain degree, hot forges well, hardens well in water, and resists brittleness. In any case pay close attention to the shapes you create in the steel, as small details make a huge difference in the performance of the tool. If you are going to buy gravers for working on steel, be sure to get good quality HSS gravers. GRS makes a good high speed steel graver, and Grobet Yellow-tang is another good choice. Avoid no-name brands and tools made in places like Pakistan. These may well be good quality, but they may not, and the price difference is not all that great. You spend so much time and care setting up and honing gravers that it really isn't worth the risk of putting all that effort into a tool that might be made of bad steel.
Getting the angles right is not all that hard, but if you can find someone with a power hone that they will let you use it will be much easier and faster. Remember that the angles are different for different tasks and materials. For inlay work you will need to pay attention to the sides of the graver as well as the face and the foot.
One final thing: Make practice pieces. I would suggest getting some pieces of scrap steel, bronze or whatever you are to be inlaying and some copper wire and sheet to punch in. This way you can try out your designs and practice your technique without using up your silver and gold.
So I hope this is helpful. Cheers.
👍: 0 ⏩: 1
taika-kim In reply to willofthewisp [2009-03-08 09:02:41 +0000 UTC]
Thanks for the reply!
Incidentally, a friend just borrowed Meek's book for me, I'm going to photograph it, the price is a bit steep... In addition, I found some books from the beginnin of 20th century at archive.org, haven't yet had time to see if they're any good. (by the way, there's a LOT of good old arts & crafts books available for free there!)
I hope I will have some excuse to spend some more time on this at the school. I think I will first buy some tools somewhere, so it will be easier to copy them afterwards. I've had always a hard time making _anything_ based on pictures & descriptions only :/ They may look right, but not perform as they should because I missed some minute detail...
By the way, good luck with your business! You seem to be living some kind of arts & crafts dream with the farm and all?-) I hope to be in a somewhat similar position some day, but in Finland, buying property is way expensive, so I'll need to work up some kind of co-operative...
👍: 0 ⏩: 1
willofthewisp In reply to taika-kim [2009-03-08 21:34:41 +0000 UTC]
Sounds like you are on your way with the engraving. There is another book that I use sometimes that has some good information. It is a bit on the older side and called Engraving on Precious Metals, by A. Brittain, S. Wolpert, and P.Morton; Arco Publishing Co.Inc. New York. It is from the 1950's and has something of a British take on engraving, but has a lot of good information about tool set up, and practice. You migh well find it on archive.org
If you do get a chance to study anything with Brian it is worthwhile. I have a friend who is planning to hitch-hike across Canada to attend one of his workshops in Ontario in May.
The ares and crafts dream is a lot of work these days. But on the other hand, with the financial world falling apart I at least have the advantage of knowing how to live on next to nothing.
Keep after it, and I'm sure you will work out the inlay thing.
Cheers.
👍: 0 ⏩: 1
taika-kim In reply to willofthewisp [2009-03-13 16:59:05 +0000 UTC]
Yeah, be as self sustainable as you can, and ignore the turmoil in the market
I think that even being your own boss is a form of self sufficiency, since you can always try to barter away the goods for food or other services to other people... And choose your own hours.
And, also, being used to being relatively poor really helps in life I think...
👍: 0 ⏩: 1
willofthewisp In reply to taika-kim [2009-03-17 04:14:27 +0000 UTC]
It is indeed a wonderful thing, in spite of all the hard work and frustration, to set my own hours, and to walk out the back door and be at work.
👍: 0 ⏩: 0
Myana [2009-02-22 13:17:09 +0000 UTC]
Hey! I've featured your deviation here: The Artisan Crafts Gallery, #60 - The best of...
feel free to hit that button on the article...
👍: 0 ⏩: 1
willofthewisp In reply to Myana [2009-02-25 21:05:12 +0000 UTC]
Thanks so much. What a great collection; looking at the other work there I'm truly in good company.
👍: 0 ⏩: 0
Soggyfoot1 [2009-01-09 22:21:17 +0000 UTC]
O my FSM.
Is that a traditional technique? carving a dovetail groove and hammering a piece of wire into it? Wouldn't have been better connected if you melted the silver and let it fill the void?
Now, as your big brother, I've got to warn you not to try to spend too much time on designs. There's wood to cut and helms to cleave...for crying out loud, that's beautiful. Is the animal supposed to be a crow/raven/corvid?
👍: 0 ⏩: 0
Azzen [2008-01-31 05:37:42 +0000 UTC]
It's for sale? I'd expect something like this to be fairly valuable. It looks like a lot of effort has been put into it.
👍: 0 ⏩: 1
willofthewisp In reply to Azzen [2008-02-02 19:43:37 +0000 UTC]
It is, and it did. This one was the third attempt. On the first I hadn't mastered the processes, and that one failed. The second ax was beautiful in every way, except that it felt clumsy and slow, so I sold it fairly cheap. This one is somehow live and moves like anything. I would consider selling it for around $4,000
👍: 0 ⏩: 1
Katterrena [2008-01-31 05:37:39 +0000 UTC]
Amazing!! I especially like the four contrasting designs near the hilt. Very beautifully done.
👍: 0 ⏩: 1
willofthewisp In reply to MBryn [2008-02-02 19:46:07 +0000 UTC]
This one was the third attempt. On the first I hadn't mastered the processes, and that one failed. The second ax was beautiful in every way, except that it felt clumsy and slow, so I sold it fairly cheap. This one is somehow live and moves like anything. I would consider selling it for around $4,000.
👍: 0 ⏩: 1
MBryn In reply to willofthewisp [2008-02-02 23:13:10 +0000 UTC]
As far as handmade weapons go, that's a really good deal. I'm only sorry that I'm a starving college student and can't buy it...yet. Someday, though, I will!
I wish I could give you more of a definitive time frame.
👍: 0 ⏩: 1
willofthewisp In reply to MBryn [2008-02-03 05:57:23 +0000 UTC]
College operates on its own special timescale.
👍: 0 ⏩: 1
willofthewisp In reply to LindseyKal [2008-02-02 19:48:51 +0000 UTC]
Thanks so much. This one was the third attempt. On the first I hadn't mastered the processes, and that one failed. The second ax was beautiful in every way, except that it felt clumsy and slow, so I sold it fairly cheap. This one is somehow live and moves like anything.
👍: 0 ⏩: 0
HEROS-ONE [2008-01-31 02:15:25 +0000 UTC]
THATS FUCKIN TIGHT!!! I WANNA MAKE ONE!!!! My spirit animal is an axe!
👍: 0 ⏩: 0
Largo222 [2008-01-31 01:17:58 +0000 UTC]
That is what a weapon should be, a piece of art. Congrats on your skill dood. I'm planning to try smithing in college, and study wesern european cultur and warfare. If I coud Ubber fave this I would.
👍: 0 ⏩: 1
willofthewisp In reply to Largo222 [2008-02-02 19:58:53 +0000 UTC]
Thanks. best of luck in school.
👍: 0 ⏩: 0
keysan [2008-01-31 01:07:07 +0000 UTC]
this is one of the best axe pieces i have seen. kudos to you. you get an instant fav!
👍: 0 ⏩: 1
| Next =>